Get reliable results with professional plastic extrusion techniques
Get reliable results with professional plastic extrusion techniques
Blog Article
A Comprehensive Overview to the Process and Advantages of Plastic Extrusion
In the vast realm of production, plastic extrusion emerges as a necessary and highly effective procedure. Translating raw plastic into continual profiles, it provides to a huge selection of sectors with its impressive convenience.
Understanding the Basics of Plastic Extrusion
While it may appear facility at very first glance, the process of plastic extrusion is fundamentally simple. The procedure begins with the feeding of plastic material, in the form of pellets, powders, or granules, right into a warmed barrel. The designed plastic is then cooled, strengthened, and reduced right into preferred lengths, finishing the procedure.
The Technical Process of Plastic Extrusion Explained
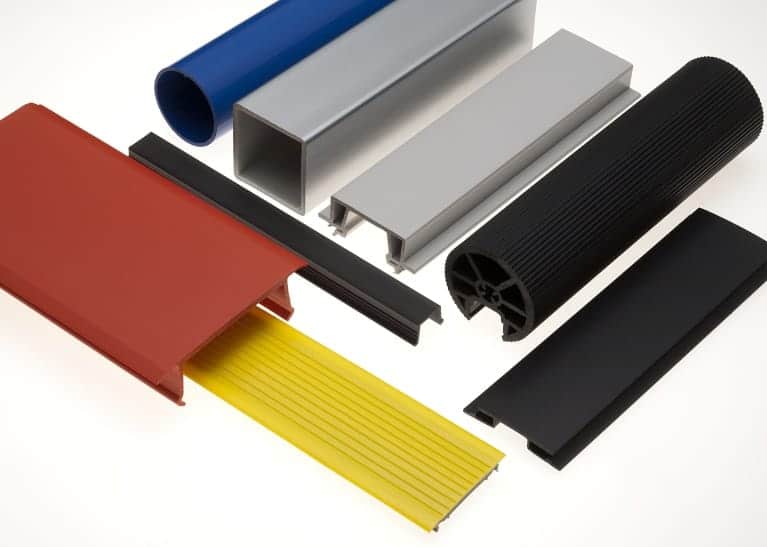
Kinds Of Plastic Suitable for Extrusion
The selection of the best kind of plastic is an essential aspect of the extrusion process. Different plastics supply unique buildings, making them much more matched to certain applications. Polyethylene, for instance, is frequently used due to its low price and very easy formability. It uses superb resistance to chemicals and dampness, making it perfect for items like tubes and containers. Polypropylene is one more prominent option due to its high melting point and resistance to exhaustion. For even more durable applications, polystyrene and PVC (polyvinyl chloride) are usually picked for their strength and toughness. Although these are usual alternatives, the choice ultimately depends upon the certain demands of the product being created. So, recognizing these plastic kinds can dramatically improve the extrusion process.
Contrasting Plastic Extrusion to Other Plastic Forming Methods
Recognizing the sorts of plastic ideal for extrusion leads the way for a broader conversation on exactly how plastic extrusion compares to other plastic developing approaches. These include injection molding, strike molding, and thermoforming. Each approach has its special usages and benefits. Shot molding, for example, is exceptional for creating intricate parts, while impact molding is ideal for hollow objects like containers. Thermoforming excels at forming shallow or large parts. However, plastic extrusion is unparalleled when it involves creating constant profiles, such as seals, gaskets, and pipes. It likewise permits a regular cross-section along the length of the item. Therefore, the selection of method greatly depends on the end-product demands and specs.
Secret Benefits of Plastic Extrusion in Production
In the realm of manufacturing, plastic extrusion offers lots of considerable advantages. One remarkable benefit is the cost-effectiveness of the procedure, that makes it an economically attractive production technique. In addition, this method supplies remarkable item flexibility and improved production rate, thereby increasing overall manufacturing performance.
Cost-efficient Production Technique
Plastic extrusion leaps to the center as an economical production technique in production. This process stands out for its capacity to create high volumes of material rapidly and effectively, providing suppliers with substantial cost savings. The key cost benefit is the ability to use less costly raw materials. Extrusion makes use of thermoplastic materials, which are less expensive compared to porcelains or metals. Even more, the extrusion procedure itself is fairly simple, minimizing labor prices. In addition, plastic extrusion needs much less power than typical production techniques, adding to reduced operational prices. The procedure also reduces waste, as any excess or malfunctioning materials can be reused and reused, giving one more layer of cost-effectiveness. On the whole, the blog monetary benefits make plastic extrusion a very eye-catching option in the manufacturing sector.

Superior Product Versatility
Past the cost-effectiveness of plastic extrusion, another considerable advantage in making lies in its superior item flexibility. This makes plastic extrusion a suitable solution for sectors that need tailored plastic parts, such as vehicle, construction, and product packaging. In essence, plastic extrusion's product versatility fosters advancement while enhancing operational effectiveness.
Enhanced Manufacturing Rate
A considerable advantage of plastic extrusion blog depends on its improved manufacturing rate. This production procedure permits high-volume manufacturing in a reasonably brief time period. It is capable of creating long, continual plastic accounts, which substantially minimizes the manufacturing time. This high-speed production is specifically advantageous in markets where huge amounts of plastic components are required within limited due dates. Few other manufacturing processes can match the speed of plastic extrusion. In addition, the ability to maintain consistent high-speed production without sacrificing product high quality establishes plastic extrusion apart from other approaches. The boosted manufacturing speed, for that reason, not only enables producers to fulfill high-demand orders yet likewise contributes to increased effectiveness and cost-effectiveness. This beneficial feature of plastic extrusion has actually made it a recommended option in many markets.
Real-world Applications and Impacts of Plastic Extrusion
In the world of production, the strategy of plastic extrusion holds profound relevance. The financial benefit of plastic extrusion, primarily its high-volume and cost-effective output, has reinvented production. The industry is persistently aiming for developments in recyclable and naturally degradable materials, indicating a future where the advantages of plastic extrusion can be maintained without endangering ecological sustainability.
Final thought
Finally, plastic go to this site extrusion is a very efficient and effective approach of changing raw products into varied items. It uses many advantages over other plastic developing techniques, including cost-effectiveness, high output, marginal waste, and layout flexibility. Its impact is greatly really felt in various industries such as construction, auto, and durable goods, making it a pivotal process in today's production landscape.
Digging much deeper into the technological process of plastic extrusion, it starts with the choice of the suitable plastic material. As soon as cooled, the plastic is cut into the required sizes or wound onto reels if the item is a plastic movie or sheet - plastic extrusion. Contrasting Plastic Extrusion to Various Other Plastic Forming Methods
Recognizing the kinds of plastic ideal for extrusion leads the method for a wider conversation on exactly how plastic extrusion piles up against various other plastic developing techniques. Couple of other production procedures can match the rate of plastic extrusion.
Report this page